With more than 25 years’ experience designing and validating fuel cell systems for myriad real-world applications, and now on its eighth generation of fuel cell stack architecture, Nuvera’s engineering team is sharing much of what it has learned about best practices in fuel cell system design. This paper draws on lessons learned over the years and questions that arise frequently with our customers and partners.
What are the main design principles in state-of-the-art fuel cell system design?
In developing electrified vehicle and machinery, OEMs and powertrain integrators must consider many critical factors, including:
- Safety and compliance with applicable standards and regulations
- Reliability and keeping equipment operational, day after day
- Durability and cost of ownership over the life of the equipment
- Efficiency and the need for lower cost operation
- Powertrain integration and the ability to quickly move vehicles from concept to production
- The need for low-cost / high-volume manufacturing capability
- Quality assurance
- Environmental impact
These considerations factor into every system developed at Nuvera, including our forthcoming 125 kW fuel cell engine.
What measures can be taken to increase the reliability of fuel cell systems?
Vehicle and machinery uptime and availability are a direct consequence of reliable critical systems and components, including the power system. Any failure can disrupt the ability for operators to do productive work, and potentially also involves troubleshooting and repair costs. Reliability is therefore a critical factor in the total cost of ownership and is a major focus at Nuvera.
Fuel cell engines must deliver similar performance, productivity, and payback as internal combustion engines. On- and off-road vehicles and equipment must meet widely varying design and performance standards, balancing reliability, durability, and cost of ownership. Leading manufactures of fuel cell engines design systems with these considerations at the forefront.
To maximize reliability, verification testing of systems and components of fuel cell engines are continuously tested for specific duty cycles and environmental conditions in purpose-built test facilities. For example, Nuvera operates a dedicated fuel cell Engine Test Module (ETM) in Osio, Italy. This testing facility allows for the remote identification and resolution of failures from test units and implementation of solutions via software updates and other means.
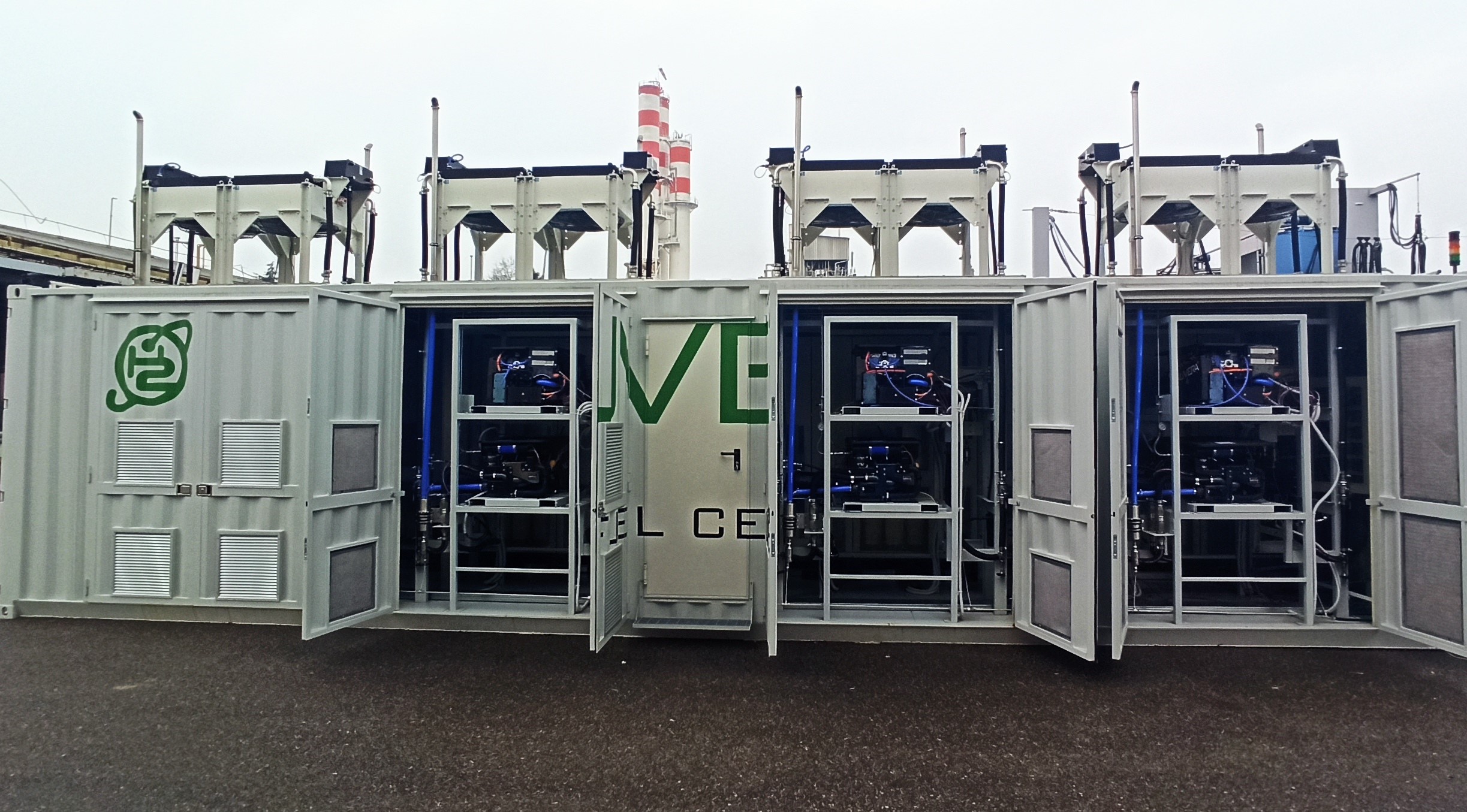
The Nuvera ETM provides the capability of simultaneously testing up to eight fuel cell engines at different customer-specific load cycles and has been an important tool in the development of current products. As a result, Nuvera fuel cell engines have demonstrated a mean time between failure (MTBF) of 2,500 hours, which is equivalent to one incident per year requiring intervention in a one-shift operation.
Which requirements need to be met to properly integrate fuel cell systems/fuel cell engines in customer use cases?
Finding the right solution for specific fuel cell use cases requires:
- Evaluating new propulsion or auxiliary technologies that match equipment operational requirements
- Identifying the most promising options for specific applications
- Meeting code requirements
- Undertaking pilot testing
Starting from scratch, this process typically involves years of planning and development by vehicle and equipment manufacturers. For this reason, it is important not only to choose a power solution based on its product specifications, but also on its ease of integration. While performance parameters are straightforward, ease of integration is less easily characterized and may be missed in comparing different fuel cell systems and providers. It is, therefore, necessary that fuel cell manufacturers clearly convey their capabilities for application analysis and for the integration of their equipment.
Leading fuel cell system manufacturers aim for customer success by providing a reliable system and one that can be easily integrated into specific hydrogen applications.
There are four key aspects that need to be provided by fuel cell system suppliers for a successful integration into their customers applications:
- Customer Access and Influence: The development and manufacturing teams are closely interacting with customers, affording them direct access to provide input that may prove useful in product design, interface, assembly, and packaging details. This input streamlines the fuel cell engine integration process by incorporating customer and end-user perspectives in product design planning and development, with customers serving as key stakeholders.
- Documentation and Training: Detailed and comprehensive documentation and training material help lead to successful and efficient vehicle and equipment integration outcomes.
- Application Assessments: Simulations and analyses, system module compatibility experiments, and controls interface experiments are conducted throughout the integration process to determine if the suggested products are a good match for the application.
- Commissioning and Support: Even after the factory acceptance test of products at a customer site, customer support is vital. Leading manufacturers work in close collaboration with their customers, providing on-going support for each unique development project.
Preconfigured fuel cell engines can significantly shorten the design and integration time required for OEMs to develop and validate fuel cell technology in on- and off-road vehicles and equipment.
What are the critical factors to deliver high quality commercially viable products at a large scale?
Robust manufacturing capabilities are a critical factor in the commercial success of fuel cell-powered vehicles and equipment. Automated production processes of fuel cell stacks and systems provide both high volume capability and quality assurance, with consistent execution of critical steps in the manufacturing process resulting in high first-pass yields.
Automated manufacturing is crucial to reducing costs both through higher yield and less waste, and the capability to manufacture at scale, further decreasing the overall cost of the equipment. The image below shows the heart of Nuvera’s automated manufacturing line, capable of producing up to 4,000 fuel cell stacks per shift annually at >97% first pass yield, dramatically increasing production capacity and product quality. Further, Nuvera can duplicate these automated lines and deploy them wherever there is demand.
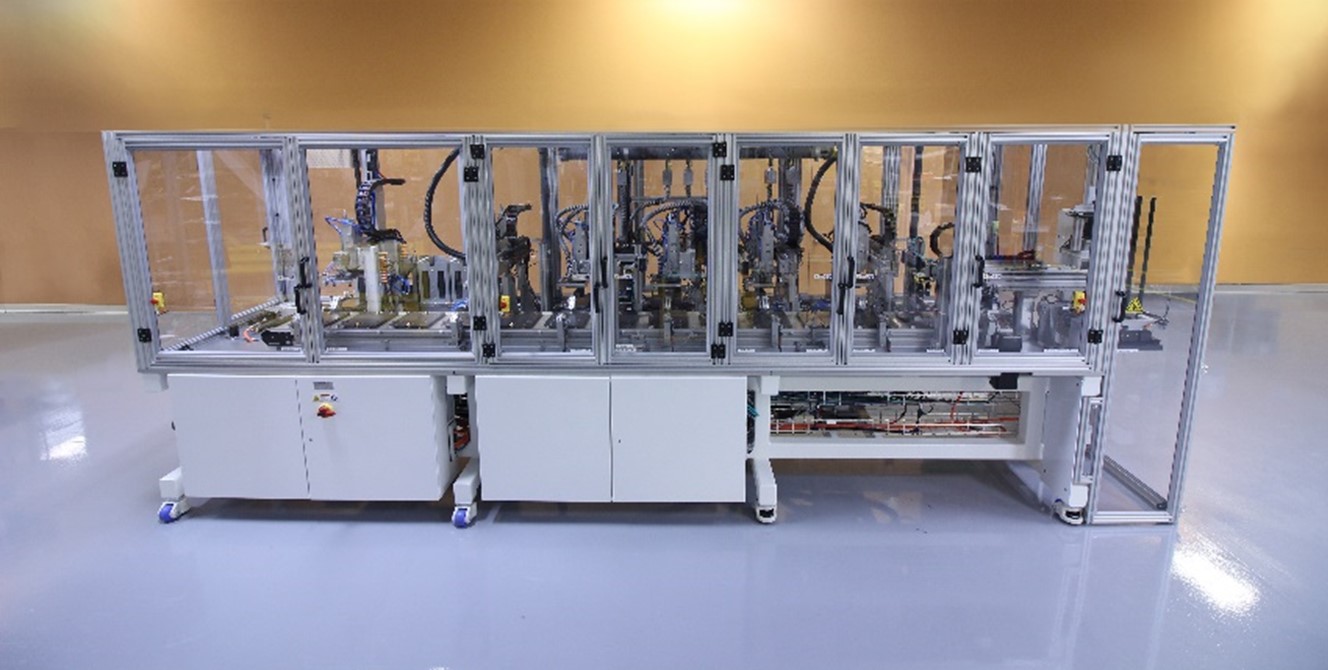
Leading manufacturers have achieved recognized industry certifications. Nuvera is ISO 9001-2015, ISO 14001-2015, and OHSAS 18001, all important standards in quality management.
Can you share a use case that embodies Nuvera’s best practices approach?
Shipping ports are concentrated sources of emissions from diesel equipment. These include carbon dioxide, the most common human-made greenhouse gas, and chemical toxins like NOx, SOx, and particulate matter, all of which are serious health hazards for workers, truckers, and residents of communities in the vicinity of ports. Given how significant the air quality impact from port equipment is, not to mention the CO2 emissions from equipment powered by internal combustion engines, eliminating diesel emissions can make a huge difference.
To reduce port emissions while maintaining the productivity of terminal operations, Nuvera partnered with Hyster-Yale Group, our parent company and a leading port equipment provider, to develop a fuel cell electric container handler called a toploader in a project funded by the California Air Resources Board. This type of vehicle is used to handle fully loaded shipping containers delivered to or leaving the port by ship, truck, or rail locomotive. There can be dozens of toploaders at a major port, and this type of equipment is typically used for at least two shifts a day. A single toploader can emit 128,000 kg of carbon dioxide per year.
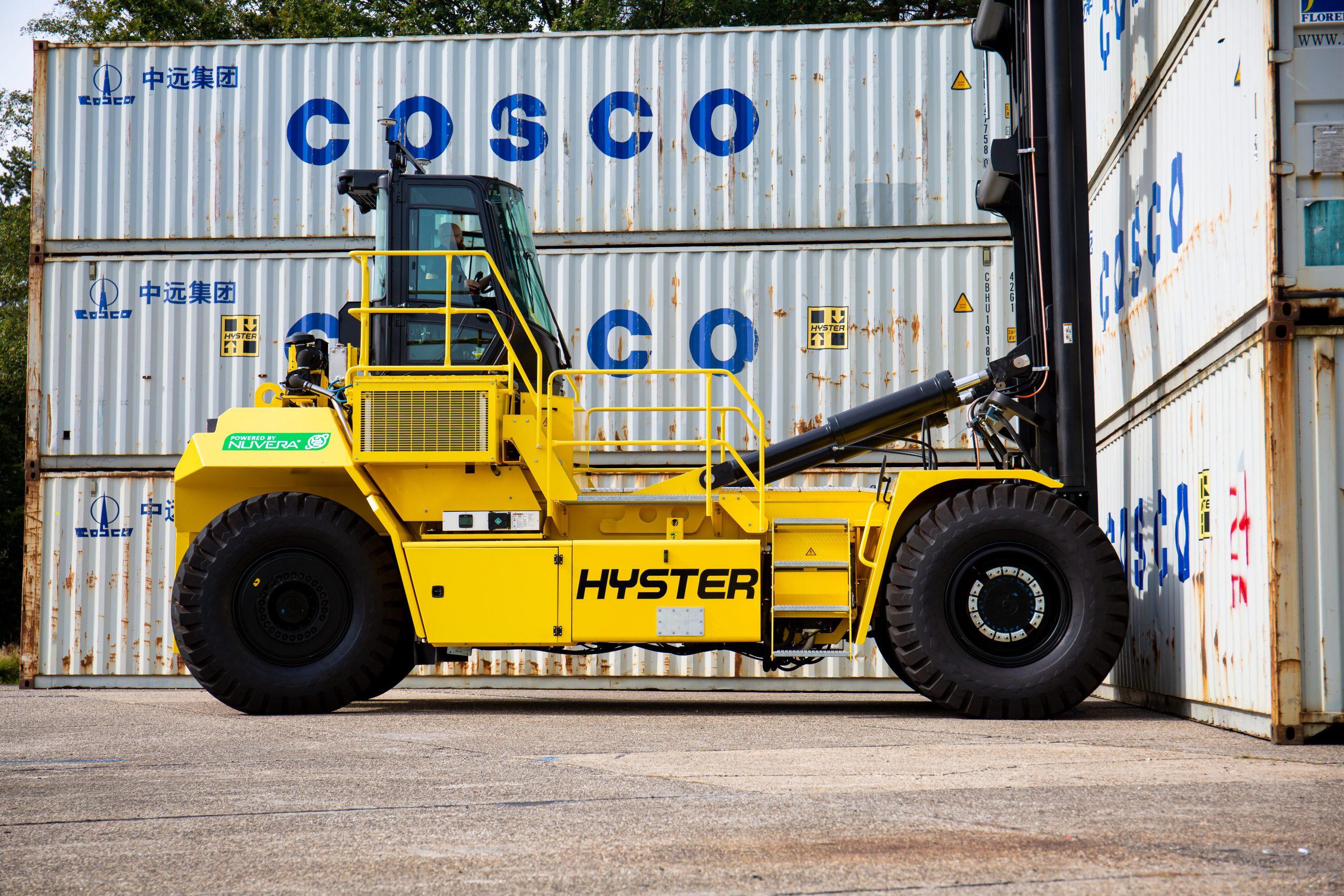
The Hyster® hydrogen fuel cell toploader developed under this project is being delivered to a terminal operator at the Port of Los Angeles and will undergo trials in daily service. This is the first step in the development of a commercially available version and is expected to be followed by other types of container handlers.
With the proper infrastructure established ― ideally providing hydrogen produced from entirely renewable sources, such as solar or wind powered electrolysis of water ― hydrogen can replace diesel in virtually every operation at a port. Our aim is to offer customers zero-emission options that perform as well as – or better than – today’s best internal combustion engines. This project has been a heavy lift for all involved (literally and figuratively!), but it has the potential to lead to greener ports in California and around the world.
Why do fuel cell systems play an important role in the energy transition?
A transition to clean power systems that meet the value, innovation, and performance needs of each application, mapping to the performance requirements of specific vehicles and equipment, is key to successful adoption of disruptive technologies. Due to their ability to power heavy commercial vehicles and industrial equipment, overall reliability, and proven success in both on- and off-road vehicle deployments, hydrogen fuel cells are a central part of today’s clean energy conversations and policy initiatives.
While hydrogen fuel cells excel in meeting the performance requirements of heavy-duty applications such as long-haul trucking, public transit, and off-road uses such as mining, agriculture, and construction, it is less well understood that fuel cells may provide the only practical zero-emission solution for many medium-duty uses that have high on-board power requirements (e.g. transport refrigeration, cement mixing, and utility trucks with auxiliary equipment), or when long recharging times are not acceptable (such as emergency vehicles).
Fuel cell engines offer motive power products the same functionality and vehicle interfaces that manufacturers expect from diesel engines – except in this case the powertrain is electric, not mechanical.
* * *
Nuvera Fuel Cells is an industry pioneer that develops advanced hydrogen technologies and transforms them into robust clean power products, enabling widespread fuel cell electric vehicle adoption. Nuvera manufactures heavy-duty fuel cell power modules for commercial and industrial use, providing products designed to meet the rigorous needs of on- and off-road vehicles and equipment. Learn more at www.nuvera.com.