Activity around new energy options to power equipment at ports is accelerating, and these first steps and use cases are showing what’s possible using hydrogen at scale.
An international workshop on the status of hydrogen and fuel cells for ports and maritime applications was held in San Francisco in September 2019. H2@Ports was convened by the U.S. Department of Energy Fuel Cell Technologies Office (FCTO), in collaboration with the U.S. Department of Transportation Maritime Administration and the European Commission Fuel Cells and Hydrogen Joint Undertaking.
More than 90 experts from government, ports and the maritime industry joined the two-day event. Participants highlighted progress, tackled challenges, and identified opportunities to exploit the potential for wide-scale hydrogen production and utilization around the world. The H2@Ports workshop is part of FCTO’s on-going H2@Scale initiative.
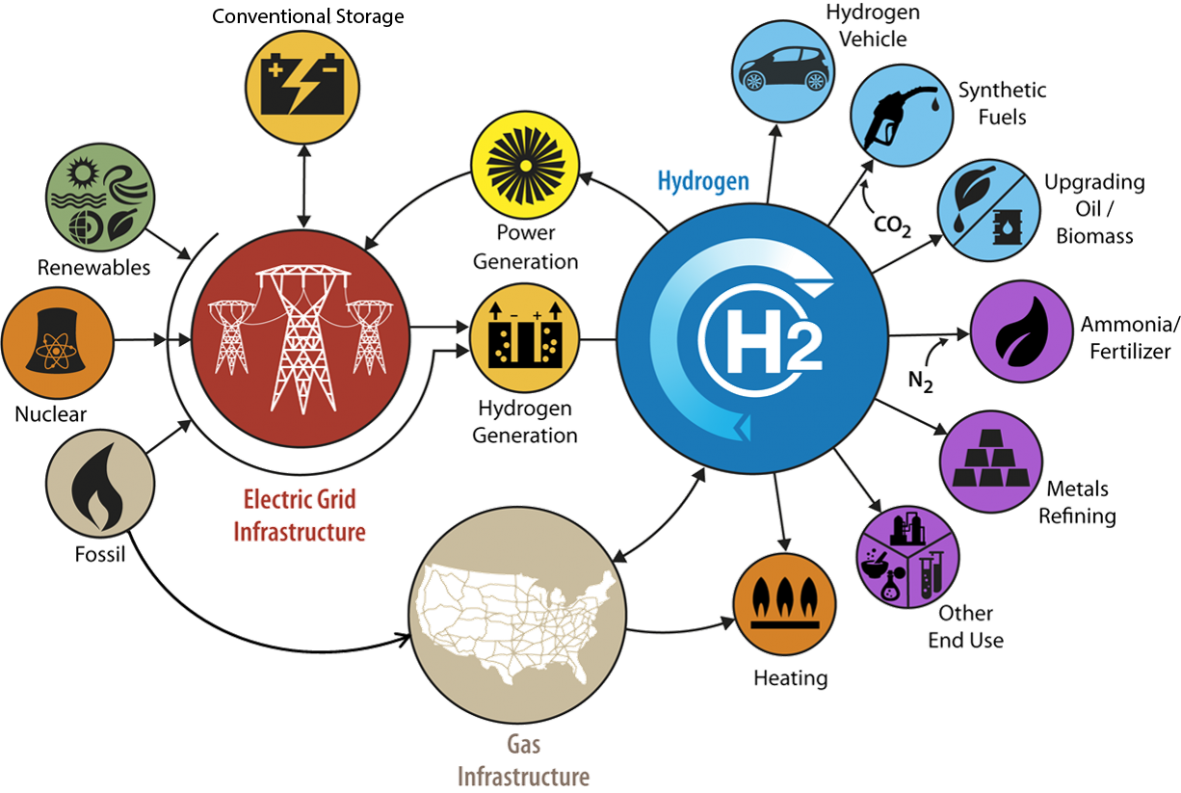
H2@Scale identifies hydrogen as an energy carrier that already serves as a critical feedstock in multiple industries. The U.S. produces more than 10 million tons of hydrogen annually, roughly one seventh of the global supply, primarily for oil refining and fertilizer. Large-scale infrastructure includes more than 1,600 miles of hydrogen pipelines, a growing network of stations, and thousands of tons of hydrogen storage in underground caverns. When production volumes are high enough and the distribution infrastructure expands to match, FCTO believes that the fueling cost for hydrogen fuel cell-powered equipment could drop to the point where the total cost of ownership is on par with – or cheaper than – conventional industrial operations.
Shipping ports are a case in point. Thousands of diesel-powered vehicles are typically in operation at a single large port. If a significant portion of these are converted to fuel cell power, lower hydrogen costs associated with high-volume consumption – nearly 300,000 tons per year at the San Pedro Bay Ports, according to Pacific Northwest National Laboratory – could make returns on investment attractive for equipment owners and operators. This effect is strongest in regions where adoption of zero-emission equipment is incentivized, or where conformance to air quality mandates is driving equipment costs up.
Gus Block of Nuvera was among the equipment providers on the H2@Ports panel, presenting the industry’s perspective on how we can address the economic and environmental and regulatory challenges currently facing port authorities and terminal operators. This involves looking closely at the application, putting data monitors on equipment, building a model and determining power and energy requirements.
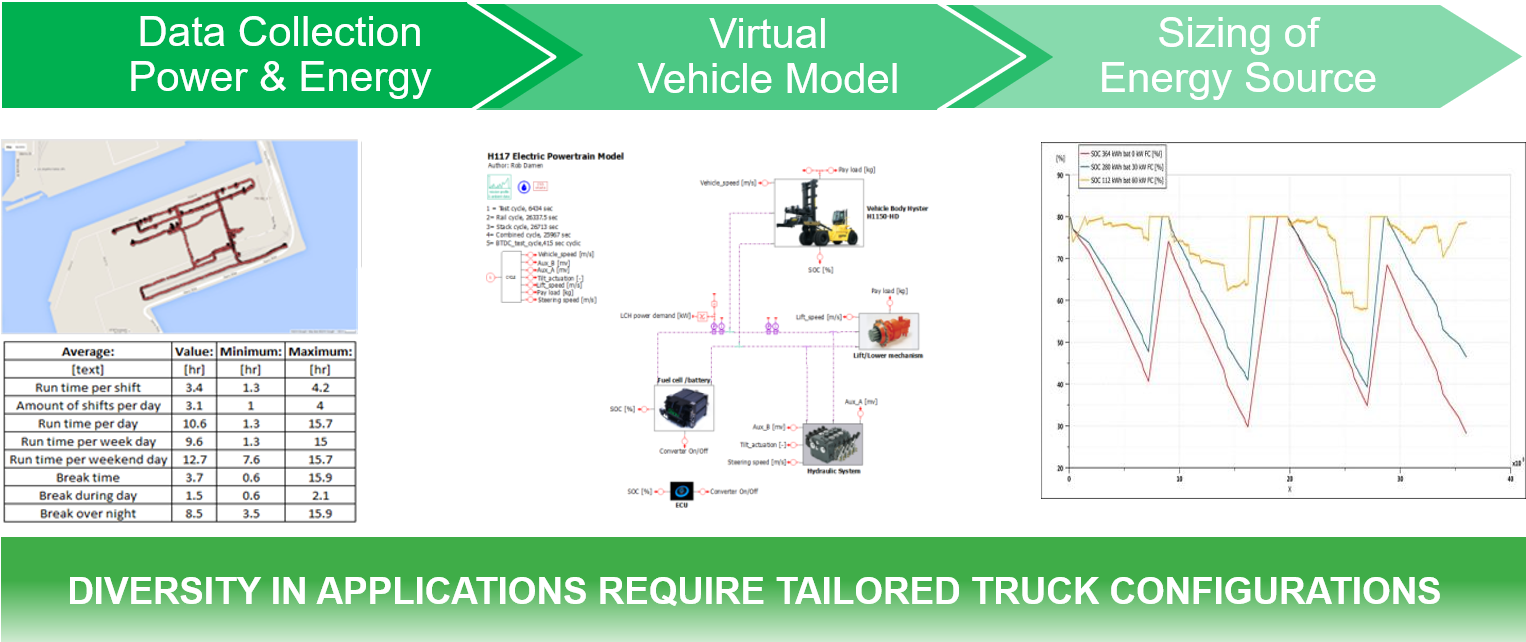
OEM Approach for Ports and Terminal Operators
As we noted in a previous blog post, vehicle electrification is the only pathway to zero-emission operation. There are two options for electric primary power: batteries and fuel cells. Engineers from Hyster-Yale Group, Nuvera’s parent company and a global industrial truck provider, found that a 400 kWh battery-electric top loading container handler would be able to meet the operational requirements of lighter duty cycles. Although the equipment may be in use 24/7, there are three breaks within each eight-hour shift that in theory allow for sufficient charging to meet the workload.
A more intensive duty cycle involving the transport of laden container to and from rail locomotives cannot rely on batteries alone, however. For the terminal operator HYG monitored, rail operated for up to seven hours with no break. This schedule does not provide enough opportunity for battery charging. It would also require more than twice the battery capacity required for the lighter duty workload, about 925 kWh. Moreover, the batteries themselves are too large to fit on board the vehicle and would diminish the allowable payload because of their weight.
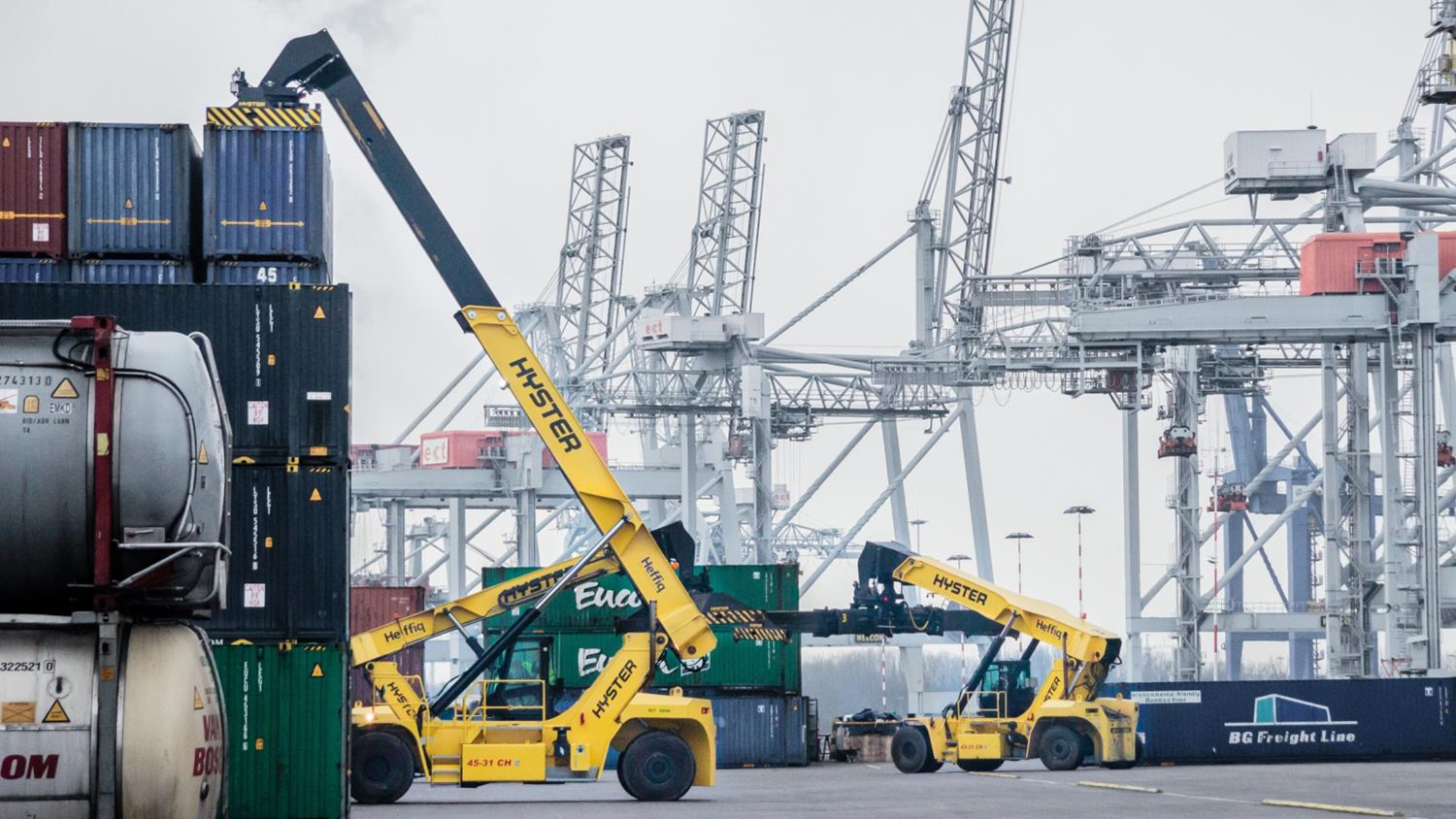
The key takeaway is that powertrain configurations must be tailored to the application. There is no “one size fits all” ─ a refrain heard multiple times at the workshop.
Global OEMs other than HYG are engaged in similar fuel cell equipment development activities. Workshop panelists summarized many recent developments, including heavy-duty hydrogen fuel cell trucks from Kenworth, Toyota and Cummins. All the presentations are available on the H2@Ports workshop website, and a summary is in preparation by Argonne National Laboratory.
Nuvera and its parent company, Hyster-Yale Group, are helping customers get ahead of the game in rapidly changing port environments. We have a long way to go before we eliminate emissions at ports. But with Nuvera fuel cell engines, fleet operators can be confident that their first steps are in the right direction.